Читайте также
07:43
В России испытали реактивный беспилотник с напечатанным на 3D-принтере двигателем
Благодаря новому способу время производства деталей сократилось в 20 раз.
Оставить комментарий
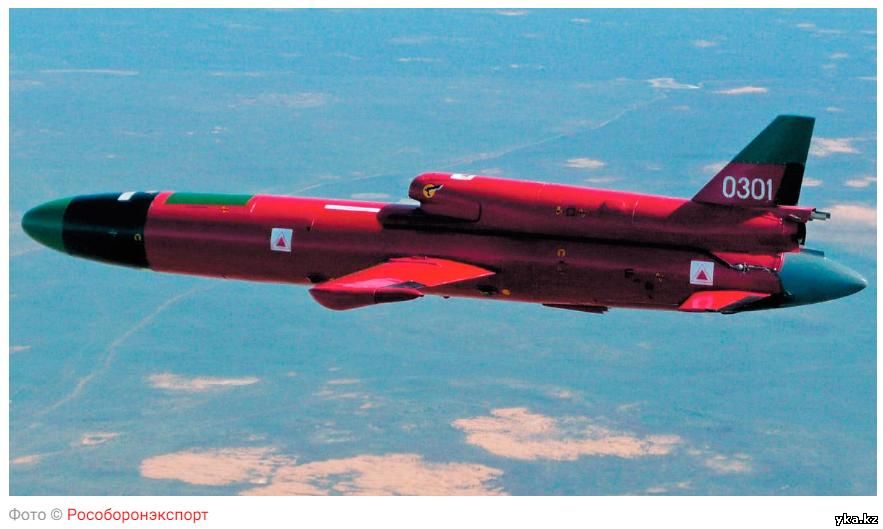
Благодаря новому способу время производства деталей сократилось в 20 раз.
Реактивный беспилотный летательный аппарат "Дань-М" совершил первый полёт с отечественным двигателем МГТД-125Э, основные детали которого были напечатаны на 3D-принтере. Испытания, состоявшиеся в Астраханской области, провёл Фонд перспективных исследований, сообщает РИА "Новости".
— Полёт "Дань-М" со взлётной массой 370 килограммов с двигателем МГТД-125Э выполнен согласно утверждённому полётному заданию, — сказано в сообщении.
Отмечается, что продолжительность полёта составила 19 минут, аппарат достиг максимальной скорости в 676 километров в час на высоте более двух тысяч метров.
В пресс-службе фонда уточнили, что новый способ позволил сократить время производства деталей до 20 раз. Кроме того, стоимость организации производства снизилась в два раза. По прочностным характеристикам ряд сплавов превосходят зарубежные аналоги более чем на 20%.
Детали, а именно элементы камеры сгорания соплового аппарата, реактивного сопла и входной части, были изготовлены из отечественных металлопорошковых высокожаропрочных композиций алюминиевых, никелевых и кобальтовых сплавов разработки Всероссийского научно-исследовательского института авиационных материалов.
Никита Могилев
Источник
Реактивный беспилотный летательный аппарат "Дань-М" совершил первый полёт с отечественным двигателем МГТД-125Э, основные детали которого были напечатаны на 3D-принтере. Испытания, состоявшиеся в Астраханской области, провёл Фонд перспективных исследований, сообщает РИА "Новости".
— Полёт "Дань-М" со взлётной массой 370 килограммов с двигателем МГТД-125Э выполнен согласно утверждённому полётному заданию, — сказано в сообщении.
Отмечается, что продолжительность полёта составила 19 минут, аппарат достиг максимальной скорости в 676 километров в час на высоте более двух тысяч метров.
В пресс-службе фонда уточнили, что новый способ позволил сократить время производства деталей до 20 раз. Кроме того, стоимость организации производства снизилась в два раза. По прочностным характеристикам ряд сплавов превосходят зарубежные аналоги более чем на 20%.
Детали, а именно элементы камеры сгорания соплового аппарата, реактивного сопла и входной части, были изготовлены из отечественных металлопорошковых высокожаропрочных композиций алюминиевых, никелевых и кобальтовых сплавов разработки Всероссийского научно-исследовательского института авиационных материалов.
Никита Могилев
Источник